Ever wondered how plastic items, from toys to appliances, are made so precisely and quickly? The answer is the THY Precision injection moulding process Step by Step. This method has changed the game, letting makers create lots of products fast and well. But what makes this process tick, and how can you make sure your moulding works best? Let’s dive into the injection moulding process step by step and find out how to balance speed and quality.
Key Takeaways
- The Injection Moulding Process Step by Step involves melting plastic pellets, injecting the molten material into a mold cavity, and then cooling it to create a solidified product.
- Understanding the Injection Moulding Process Step by Step is crucial for optimizing speed and quality in plastic manufacturing.
- Factors such as injection pressure, melt temperature, and cooling time must be carefully balanced to ensure consistent, high-quality results.
- Mold design and the selection of the right thermoplastic material are also critical elements in the injection moulding process step by step.
- Mastering the machine setup and maintaining proper maintenance are essential for maximizing the efficiency of your injection moulding operations.
Understanding the Fundamentals of InjectionMouldingProcessStepByStep
At THY Precision, we know the detailed steps of the injection moulding process step by step. This method has many important steps that work together to make high-quality parts. We’ll look into the basics of this method and see how it mixes speed with quality.
The Injection Moulding Cycle
The injection moulding cycle has several key steps. Each step is crucial for the process. These steps include mold close, injection, pack/hold, cooling/plasticizing, mold open, and part ejection. By controlling each step well, manufacturers can make the injection moulding process step by step work better for their needs.
Balancing Speed and Quality
Finding the right mix of speed and quality is key in the injection moulding process step by step. Important factors like injection speed, injection pressure, melt temperature, and cooling time need to be set right for quality parts. Injection speed affects how the plastic fills the mold. Injection pressure and melt temperature affect the part’s strength and look. Cooling time is key for keeping the part stable and maintaining quality and consistency.
At THY Precision, our experts know how to balance the injection moulding process step by step for the best results. By watching and adjusting these key factors, we make parts that are top-notch in quality and performance.
“Achieving the perfect balance between speed and quality is the hallmark of a truly masterful injection moulding process Step by Step.”
Designing the Mold: A Critical Step
The design of the mold is key in the THY Precision injection molding process Step by Step. Engineers use advanced CAD software to make a detailed 3D model of the part. They focus on the best plastic flow, efficient cooling, and easy ejection. They also consider the mold material, the part’s details, and the machine’s abilities.
A well-designed mold is crucial in the THY Precision injection molding process Step by Step. It can make thousands or even millions of identical parts with great precision. The mold is made from hardened steel or aluminum and is precisely machined to match the product’s features. This careful detail makes THY Precision stand out, ensuring top-quality products.
In the THY Precision injection molding process Step by Step, designing the mold is a complex task. Engineers pay close attention to several factors:
- Plastic flow and distribution in the mold cavity
- Efficient cooling to help the part solidify properly
- Smooth ejection of the finished product
- Compatibility with the mold material and the machine’s capabilities
By excelling in mold design, THY Precision ensures high-quality parts that meet their clients’ strict standards. Their focus on detail and excellence makes them a leader in the industry.
Selecting the Right Thermoplastic Material
Choosing the right thermoplastic material is key in the InjectionMouldingProcessStepByStep. Materials like polypropylene, polyethylene, and ABS are often used. The material you pick depends on what you want the final product to be like. This includes things like strength, flexibility, and how it handles heat and chemicals.
Knowing about material properties is crucial for a good outcome in the InjectionMouldingProcessStepByStep. Picking the right thermoplastic lets you fine-tune the final product’s features. This way, you get the performance you need.
Factors to Consider in Thermoplastic Material Selection
- Strength and durability
- Flexibility and impact resistance
- Thermal and chemical resistance
- Aesthetic properties, such as color and finish
- Cost and availability
Each thermoplastic material, like polypropylene, polyethylene, and ABS, has its own set of properties. These can be adjusted to fit the InjectionMouldingProcessStepByStep’s needs. By looking at these factors, you can pick the best material for your project. This ensures the InjectionMouldingProcessStepByStep goes smoothly.
Thermoplastic Material | Typical Properties | Common Applications |
---|---|---|
Polypropylene (PP) |
|
|
Polyethylene (PE) |
|
|
Acrylonitrile Butadiene Styrene (ABS) |
|
|
Understanding the unique traits and uses of these thermoplastics helps you make a smart choice during the InjectionMouldingProcessStepByStep. This way, you can pick the best material for your project. This ensures the process goes well.
“The right material selection is the foundation of a successful InjectionMouldingProcessStepByStep. It’s not just about choosing a material, but understanding how it will perform and interact with the process.”
Mastering the Machine Setup
At THY Precision, we know the injection molding process is all about finding the right balance. Getting the injection molding machine ready is key to making top-quality products. This means setting up the mold, adjusting the temperature, and calibrating the pressure right.
First, you must install the mold on the machine correctly. It’s important to understand how the machine’s clamping unit works and what your mold needs. A secure, precise fit helps avoid mold problems during the process, making your products better.
Then, adjust the machine’s barrel and nozzle temperatures. These temperatures affect how the plastic flows. If you get it right, you’ll get a smooth fill. But if not, you might have problems with your parts.
Lastly, calibrate the machine’s injection unit carefully. Adjusting the pressure lets you control how fast and hard the plastic goes into the mold. This is key for making parts the right size and quality.
At THY Precision, we know setting up the machine right is vital. By focusing on mold installation, temperature, and pressure, you can make your injection molding work better. This way, you’ll make parts that your customers will love.
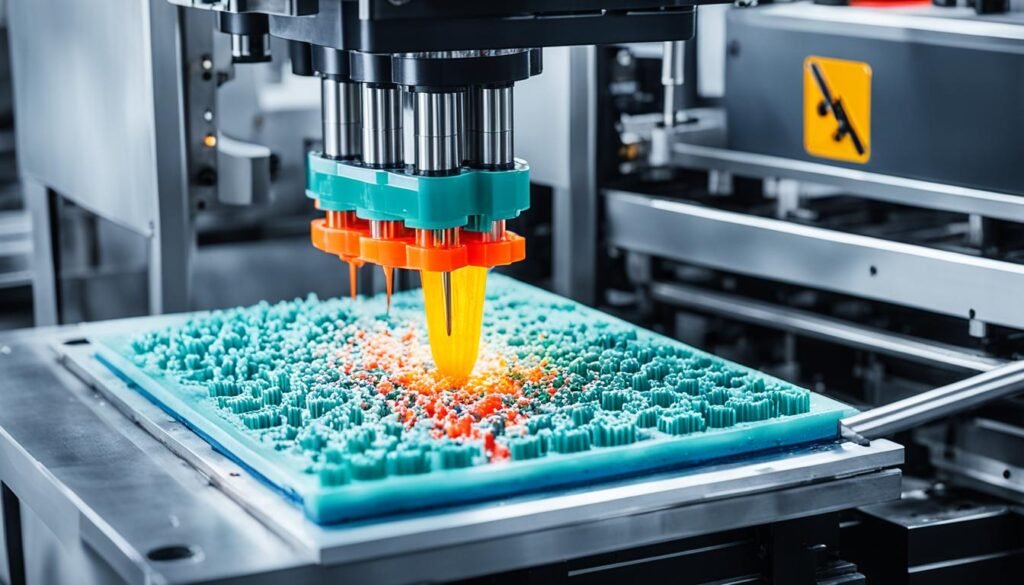
Injection Molding Process Step | Key Considerations |
---|---|
Mold Installation | Secure fit, minimizing leakage and mold shifting |
Temperature Setting | Optimal barrel and nozzle temperatures for material viscosity and flow |
Pressure Calibration | Precise control of injection pressure for desired part geometry and accuracy |
“Mastering the injection molding machine setup is the foundation for consistently producing high-quality parts. At THY Precision, we take this step seriously to ensure our customers receive the best possible products.”
Melting and Molding: The Heart of the InjectionMouldingProcessStepByStep
The injection molding process is a complex dance. It’s all about precision and control. The key steps include injection pressure, holding pressure, nozzle pressure, and mold locking pressure. These steps ensure the final product is top-notch.
Injection Pressure
Injection pressure is the force that pushes molten plastic into the mold. It’s measured in PSI or MPa. Getting this pressure right is crucial for a perfect fill and to avoid waste or damage.
Melt Temperature
The melt temperature is how hot the plastic needs to be for injection. It’s vital for smooth flow, cooling, and quality. Keeping this temperature steady is key for a great product.
THY Precision masters the balance of key pressures and temperatures. This ensures a smooth process and high-quality products. Their focus on detail and improvement makes them leaders in the industry.
Cooling and Ejection: The Final Stages
The final stages of the InjectionMouldingProcessStepByStep are crucial for quality and stability. Cooling time is key to solidifying the plastic in the mold. This prevents issues like warping or shrinkage.
As the part cools and hardens, it keeps its shape and size. The cooling time must balance speed and quality. Too little cooling can cause distortion, while too much slows down production.
After solidifying, the mold opens, and the part is ejected with ejector pins. Ejection needs precise control to avoid damage. It’s important for the part’s quality and getting the mold ready for the next cycle.
Key Factors | Importance |
---|---|
Cooling Time | Ensures dimensional stability and minimizes defects like warping or shrinkage. |
Clamping Force | Proper control ensures the part is released cleanly without damage. |
Ejection Process | Crucial for maintaining the part’s integrity, surface finish, and preparing the mold for the next cycle. |
Managing the cooling and ejection stages well makes high-quality parts with great stability and surface finish. This focus is key for meeting industry demands and keeping customers happy.

Conclusion
The injectionMouldingProcessStepByStep has changed how we make plastic parts. It lets manufacturers balance speed and quality. This way, they can make products that meet today’s market needs.
THY Precision leads in plastic manufacturing. They keep making their injectionMouldingProcessStepByStep better. They use new tech and always aim to improve. This has made their production faster, their quality better, and their work more productive.
As we need more plastic parts, the injectionMouldingProcessStepByStep is more important than ever. Companies like THY Precision use this process to meet customer needs. They make high-quality products quickly and reliably. The future will bring more improvements to this process, making it even more vital for plastic manufacturing.